Answer:
In Star vs. Delta: Delta configuration is preferred over star configuration in motor applications due to its ability to provide higher starting torque, reduced voltage drop, simplified control, reduced current imbalance, space and weight considerations, potential cost efficiency, and suitability for induction motors requiring higher starting torque.
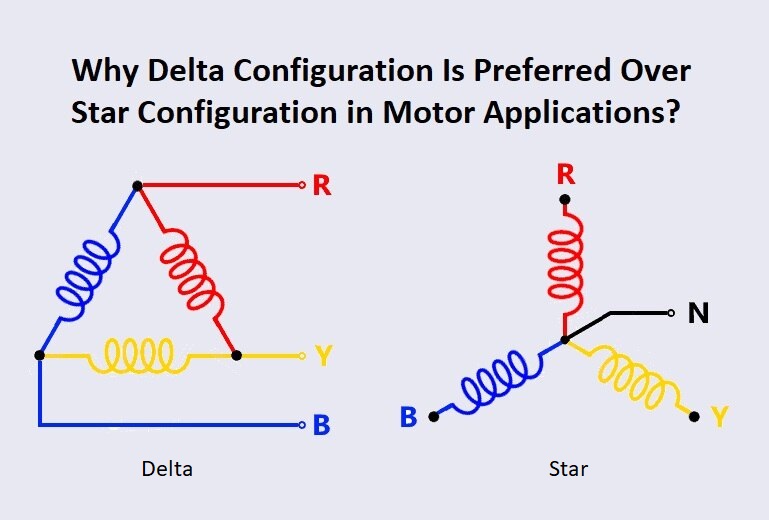
Reasoning:
Delta configuration is favored over star configuration in motor applications for several compelling reasons:
- Higher Starting Torque: The delta configuration delivers higher starting torque, making it well-suited for applications requiring the motor to initiate motion under heavy loads or demanding conditions. This enhanced torque is vital for ensuring efficient motor operation when dealing with initial resistance.
- Reduced Voltage Drop: With its inherent higher line-to-line voltage compared to the star configuration, the delta configuration minimizes voltage drop over extended distances. This feature is particularly advantageous in scenarios where power transmission occurs over substantial cable lengths, maintaining more consistent and reliable motor performance.
- Simplified Control: The delta configuration offers simpler control mechanisms, facilitating the achievement of specific performance objectives such as speed control, dynamic braking, and responsive adjustments. This streamlined control contributes to efficient motor operation and responsive system behavior.
- Reduced Current Imbalance: In the delta configuration, circulating currents are naturally lower than those in the star configuration. This reduced current imbalance between phases enhances overall system efficiency and helps prevent uneven heating of motor windings, thereby extending the motor’s operational lifespan.
- Space and Weight Considerations: Due to its fewer conductors and connections, the delta configuration lends itself to more compact installations. This advantage is crucial in applications where space is limited, and weight constraints need to be adhered to, allowing for greater flexibility in motor placement and system design.
- Potential Cost Efficiency: Depending on the specific motor design and application requirements, the delta configuration can lead to potential cost savings. The simplified circuitry and reduced need for additional components may contribute to a more economical motor solution without compromising performance.
- Suitability for Induction Motors: Induction motors often necessitate higher starting torque for efficient operation, especially when dealing with heavy loads or challenging conditions. The delta configuration aligns well with these requirements, making it a suitable choice for induction motors that require enhanced starting performance.
In essence, the delta configuration’s ability to provide higher starting torque, minimize voltage drop, simplify control mechanisms, reduce current imbalances, accommodate space constraints, potentially lower costs, and cater to the needs of induction motors positions it as a preferred choice in various motor applications.
FAQs
Why would one choose a star (Y) connection over a delta (Δ) connection in a three-phase system?
For simplified ground reference and balanced loads.
In which situations is a delta connection preferred over a star connection for motor applications?
When higher starting torque and reduced voltage drop are needed.
What advantages does a star connection offer in terms of voltage balancing compared to a delta connection?
Improved line-to-neutral voltage balance.
Are there specific cases where a delta connection is favored over a star connection for power transmission in high-voltage networks?
Yes, when reduced insulation requirements and costs are essential.
How does the choice between a star and delta connection impact the ability to control and adjust impedance in a circuit?
It affects the ease of impedance adjustments.
When might a delta connection be more suitable than a star connection for managing harmonics and improving power quality?
In scenarios where lower harmonics are desired.
What considerations influence the decision to use a star or delta connection in terms of fault tolerance and system reliability?
Ease of isolating faulty components and continued operation.
In terms of space utilization and compactness, under what circumstances is a delta connection preferred over a star connection?
When fewer conductors and connections are needed.
How does the choice between a star and delta connection affect the efficiency and energy consumption of a three-phase motor or generator?
It impacts the motor’s starting torque and overall performance.
Are there instances where a hybrid configuration (both star and delta connections) is preferred over using either connection type exclusively?
Yes, for optimizing specific performance requirements.