Permanent-Magnet Synchronous Motors (PMSM)
Introduction
Permanent-Magnet Synchronous Motors (PMSMs) are a type of synchronous motor that uses permanent magnets embedded in the steel rotor to create a constant magnetic field. The stator, typically made of laminated steel with windings, produces a rotating magnetic field when powered by an alternating current (AC). The rotor then locks onto this rotating magnetic field and rotates at the same speed, maintaining synchronous speed.
PMSMs are known for their high efficiency, high power density, and good performance characteristics, making them suitable for a wide range of applications including electric vehicles, industrial automation, robotics, and aerospace.
Operating Principle
The key principle behind the operation of a PMSM is the interaction between the magnetic field generated by the stator windings and the magnetic field of the permanent magnets on the rotor. When AC power is supplied to the stator, it generates a rotating magnetic field. The permanent magnets on the rotor are attracted to this rotating field, causing the rotor to spin at the same frequency as the stator field.
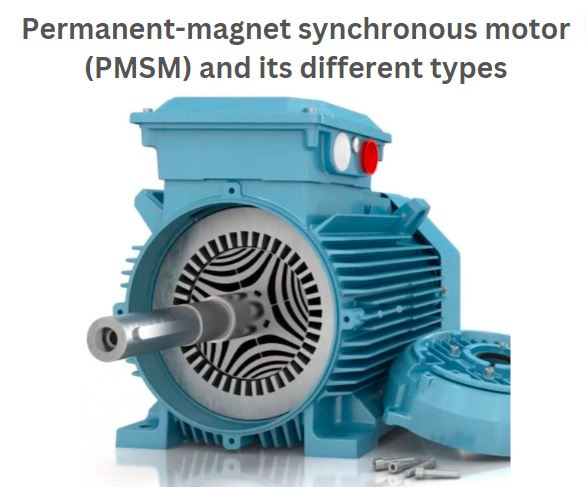
Advantages of PMSMs
- High Efficiency: Due to the absence of rotor windings, there are no rotor copper losses, leading to higher efficiency.
- High Power Density: Permanent magnets provide strong magnetic fields without the need for additional power, allowing for a compact motor design.
- High Reliability: With fewer moving parts and no brushes, PMSMs are more reliable and require less maintenance.
- Precise Control: PMSMs offer excellent performance in applications requiring precise speed and position control.
Disadvantages of PMSMs
- Cost: The use of rare-earth permanent magnets can make PMSMs more expensive than other motor types.
- Temperature Sensitivity: Permanent magnets can lose their magnetic properties at high temperatures.
- Complex Control Systems: PMSMs require sophisticated control systems to operate efficiently, often involving vector control or field-oriented control.
Types of PMSM
PMSMs can be classified based on the rotor design and the arrangement of the permanent magnets. The main types are:
- Surface-Mounted Permanent-Magnet Synchronous Motor (SPMSM)
- Interior Permanent-Magnet Synchronous Motor (IPMSM)
Surface-Mounted Permanent-Magnet Synchronous Motor (SPMSM)
In SPMSMs, the permanent magnets are mounted on the surface of the rotor. This design is simpler and easier to manufacture. SPMSMs are known for their high-speed capabilities and are often used in applications where the motor needs to run at high speeds, such as in certain types of pumps and compressors.
Advantages:
- Easier to manufacture.
- Good for high-speed applications.
- Simple rotor construction.
Disadvantages:
- Weaker mechanical strength due to magnets being on the surface.
- Lower torque density compared to IPMSMs.
Interior Permanent-Magnet Synchronous Motor (IPMSM)
In IPMSMs, the permanent magnets are embedded within the rotor. This design provides better mechanical strength and higher torque density. IPMSMs are commonly used in applications requiring high torque and robustness, such as electric vehicles and industrial drives.
Advantages:
- Higher torque density.
- Better mechanical strength.
- Improved performance at low speeds.
Disadvantages:
- More complex and costly to manufacture.
- Increased risk of demagnetization under high stress.
Features and Applications of the PMSM
- High Efficiency: PMSMs operate with high efficiency, especially at partial loads, due to the reduced electrical losses in the rotor.
- Precise Control: The design of PMSMs allows for precise speed and position control, which is crucial in applications like robotics and CNC machinery.
- High Power Density: PMSMs deliver a higher power output relative to their size compared to other types of motors, making them ideal for applications where space is limited.
- Low Maintenance: With no brushes or commutators, PMSMs have fewer wear parts and thus require less maintenance, leading to lower operational costs.
- Reduced Heat Generation: The absence of rotor windings and the high efficiency result in less heat generation, enhancing the reliability and lifespan of the motor.
Applications of PMSMs
PMSMs are used in a variety of applications due to their high efficiency, reliability, and performance characteristics:
- Electric Vehicles: PMSMs are widely used in electric and hybrid vehicles due to their high power density and efficiency.
- Industrial Automation: PMSMs provide precise control, making them ideal for robotics, CNC machines, and automated production lines.
- Aerospace: High efficiency and reliability make PMSMs suitable for aerospace applications, including actuators and auxiliary power units.
- Renewable Energy: PMSMs are used in wind turbines and other renewable energy systems due to their high efficiency and robust design.
Conclusion
Permanent-Magnet Synchronous Motors (PMSMs) are a critical technology in modern electric motor applications. With their high efficiency, power density, and reliable performance, PMSMs are well-suited for a wide range of demanding applications. Understanding the different types of PMSMs, such as SPMSMs and IPMSMs, helps in selecting the right motor for specific needs, balancing factors like cost, complexity, and performance.